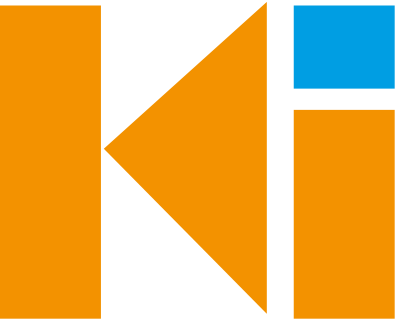
Wear Resistant Systems for Construction
Maintain plant efficiency and integrity with Kingfisher Industrial
Plant degradation – we understand the pain
Virtually all materials and components used in the building and construction industry start life as a mined mineral prior to its primary or secondary production process. In handling these minerals, the consequence of plant degradation is an ever present problem to the manufacturers of building materials. From receipt of raw or semi-processed materials at the gatehouse to dispatch of the finished product, the task of combating wear is a constant thorn in the side of plant engineers and the resources available to them.
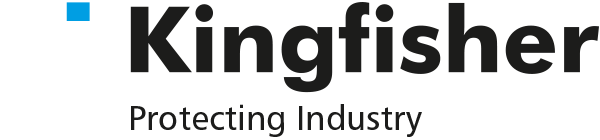
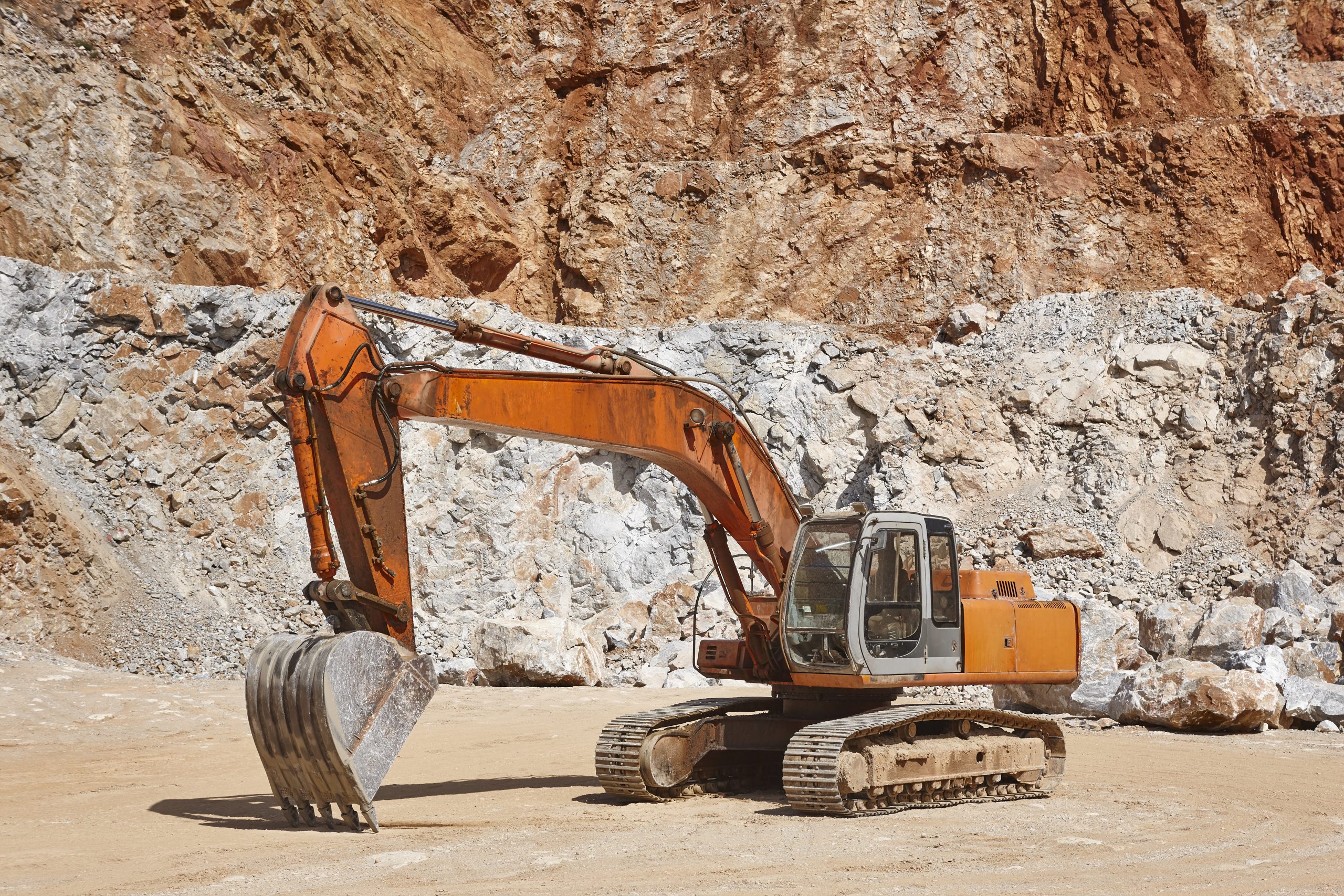
Maximise production efficiency and costs
By implementing proven engineering practice to protect process plant and equipment, plant managers can anticipate a greater return on investment. As most products are manufactured in continual processes in order to maximise production efficiency and cost control, the availability of that equipment is paramount to the operation’s effectiveness.
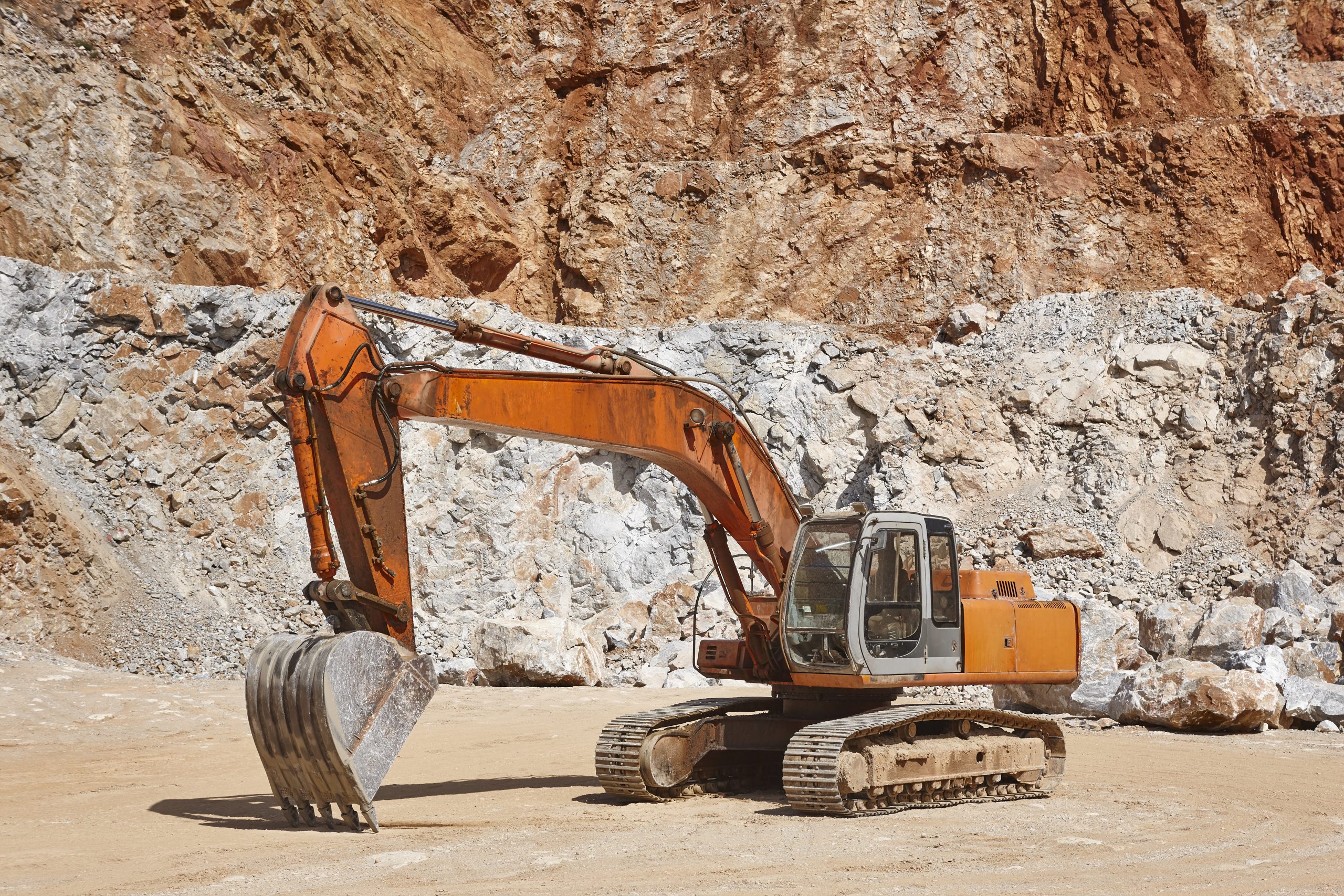
Maximise production efficiency and costs
By implementing proven engineering practice to protect process plant and equipment, plant managers can anticipate a greater return on investment. As most products are manufactured in continual processes in order to maximise production efficiency and cost control, the availability of that equipment is paramount to the operation’s effectiveness.
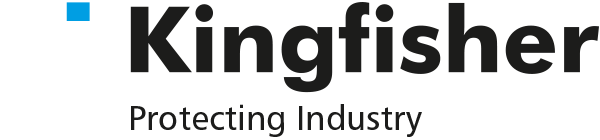
The Solution Providers
Silos, pipework, mixers, dryers, hoppers and transfer chutes all benefit from protection by materials designed to combat the effects of handling volumes of minerals within a continual or batched operation.
Protection over replacement
See below an example how Kingfisher Industrial can help with Wear Protection within the Construction industry
Problem
Loading and moving abrasive materials like sand, cement and clay at a building product site often results in material accumulation on essential equipment. In a specific case, the front-loading bucket was handling a clay type material, known for its sticky nature. When the loading shovel bucket was emptied a large amount of the clay remained built up inside the bucket and the loading shovel bucket failed to fully discharge.
Solution
The Kingfisher technical team conducted a thorough inspection of the loading shovel buckets and proposed a practical solution. Kingfisher recommended the installation of a fully tailored K-PLAS inner lining system to prevent material adhesion inside the bucket. The K-PLAS polymer lining solution, with its low friction characteristics, effectively prevents material from sticking to the bucket’s surface, thereby minimisng material build-up and the requirement for frequent manual cleaning.
Benefit
Opting for our retrofit wear-resistant lining solutions not only helps in the maintenance of existing process plant and equipment, crucial for keeping the plant operational, but also proves to be a cost-effective measure.
Key Benefits
Reduce material build-up & carry-back
Eliminate cost to repair
Improve process efficiency
more examples
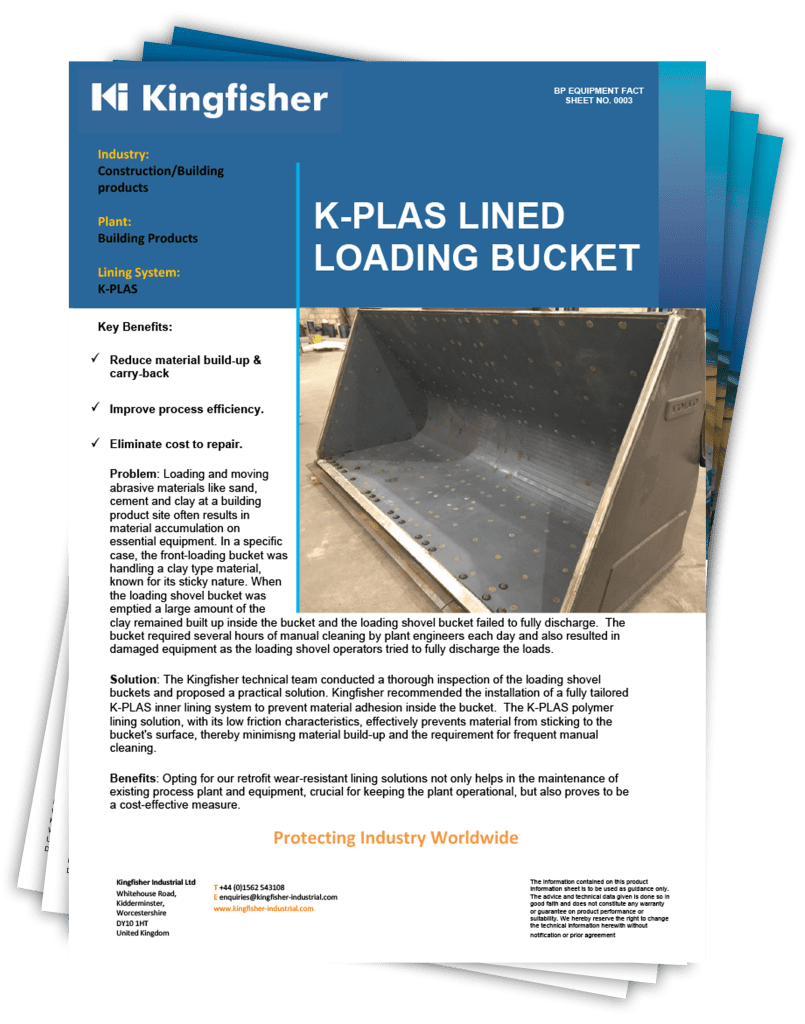
View more case studies
If you’d like to see more case studies showing how we Kingfisher help solve problems and find solutions within the Construction industry, please register your interest and we will get in touch.
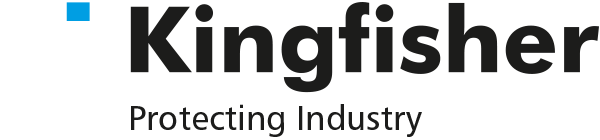
Wear Protection
Kingfisher offer a full range of ceramic, metallic and polymer lining systems. With our experience protecting process plant and equipment in many industrial applications and the performance knowledge of the materials we provide we offer a totally unbiased solution for each individual application.
Ceramic
Metallic
Polymer