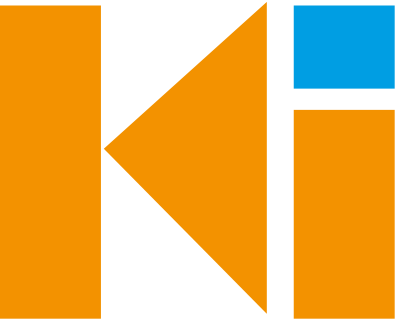
Wear Resistant Systems for Quarrying
Maintain plant efficiency and integrity with Kingfisher Industrial
Plant degradation – we understand the pain
Handling vast amounts of minerals from the quarry to the truck or railhead, involves many different processes and generates a host of problems that have to be overcome. During the many stages of operation, the activities associated with the process such as crushing, washing, screening and classifying are in direct contact with these minerals and all suffer as a consequence. Dependant on the type, size and volume, processing these minerals will cause the equipment to degrade due to abrasive characteristics of its makeup. Regardless of what minerals are being handled and dependant on their Mohs hardness, this rating will determine the extent of investment needed to protect the plant and equipment from premature failure.
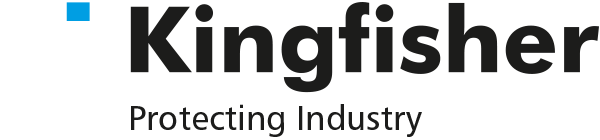
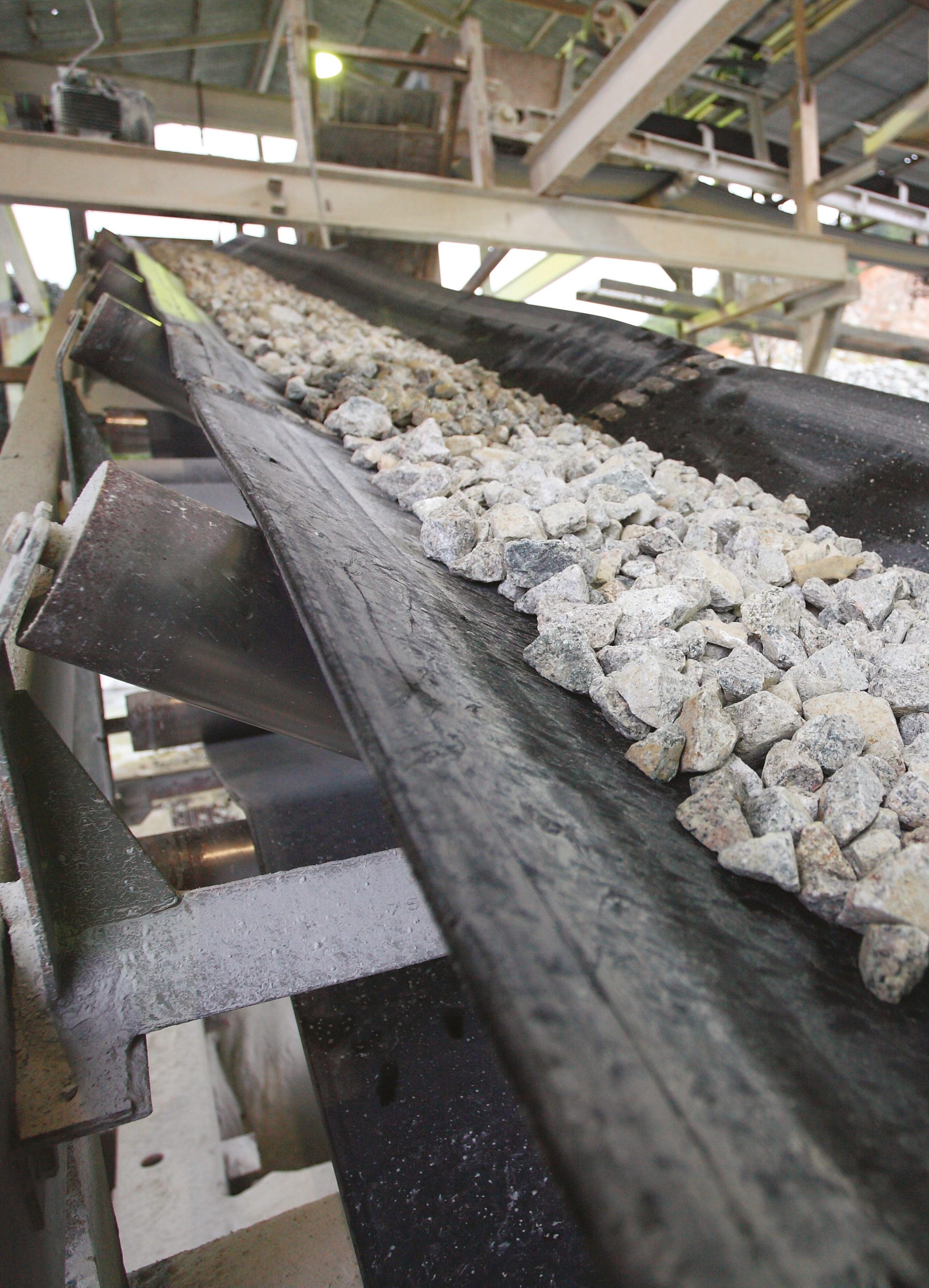
Increase plant efficiency and service longevity
Traditionally, metallic materials such as QT, and manganese plate and castings have been used around the different crushing operations where the product is handled and crushed down to a minus sized aggregate. As further processing is undertaken for sand and small aggregate, polymer type materials such as rubber and polyurethane operating in a hydraulic state have been used with great success. As with all solutions to problems, careful consideration has to be given in identifying what unique issues associated with grades and mineral types are prevalent as a ‘one size fits all’ approach very rarely succeeds.
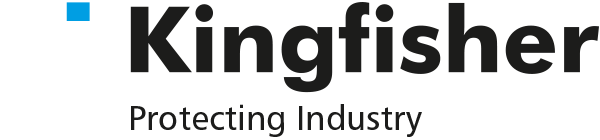
The Solution Providers
In identifying all relevant wear criteria and referencing a huge portfolio of wear protection materials and techniques, Kingfisher is able to make sound recommendations supported by firm performance guarantees. This option reduces the inherent risk of uneconomic investment as the costs of replacement can sometimes outweigh the initial CAPEX cost.
Protection over replacement
See below an example how Kingfisher Industrial can help with Wear Protection within the Quarrying industry
Problem
The granite handled at Mountsorrel is among the hardest known. Unfortunately, this fact was being brought home by the excessive levels of wear that were being experienced in the storage hoppers and conveyor transfer points at the railhead. The existing steel and rubber liners used within the system were not lasting six-months, due to the high levels of impact and sliding induced abrasion from handling the granite. This was resulting in high maintenance and repair costs, as infrastructure needed replacing frequently.
Solution
The top section of the sloping walls of the storage hoppers were subject to sliding abrasion, but the bottom sloping walls and discharge sections suffer from both sliding and impact induced abrasion. The combination that we chose had proven itself over long periods in very demanding applications. It comprised of our 40mm thick K-BAS, cast basalt lining, for the top sloping section of the hopper sides, and our 50mm thick 92P K-ALOX ceramic liners on the high wear areas in the bottom sloping and discharge chute sections… (read full case study for more info)
Benefit
Upon speaking to the an engineer from Mountsorrel, he said, “We were repairing the old lining system within the original hoppers all the time and also having to patch the structure itself, however, since Kingfisher installed their
Key Benefits
Improved Wear Resistance
Maintain blending capacity
Prevention of material build-up
Cheaper than replacing
Internal liner can be repaired in position
Out performs traditional liners by a factor of 6-8 times
more examples
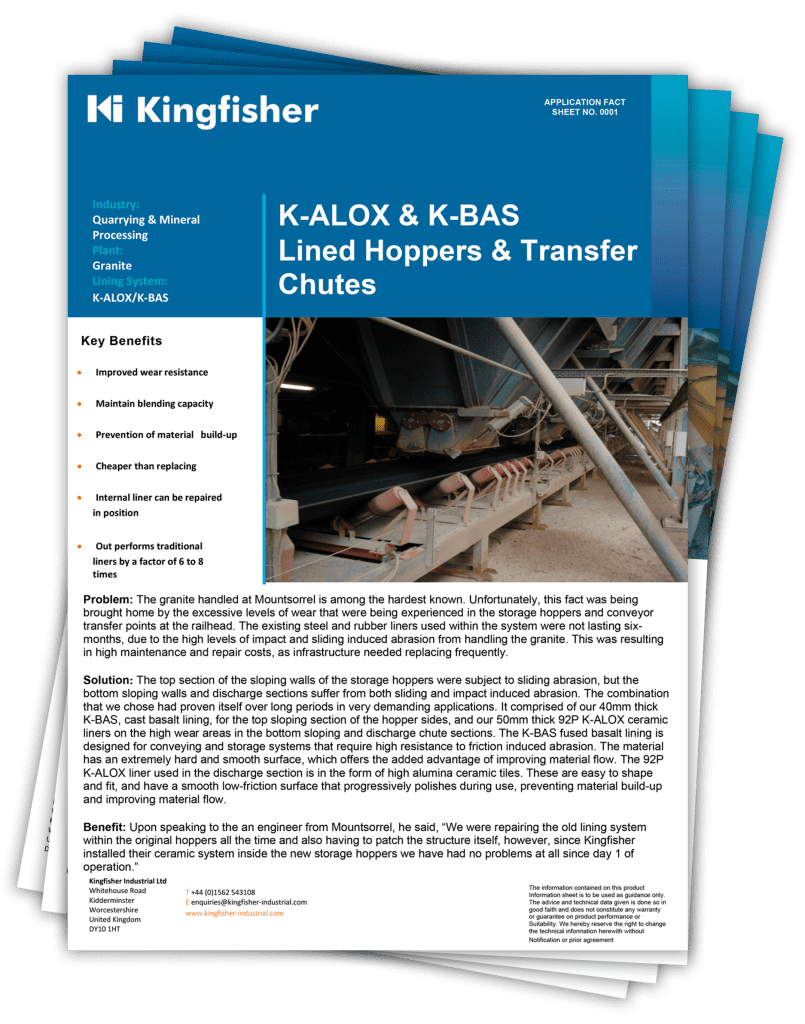
View more case studies
If you’d like to see more case studies showing how we Kingfisher help solve problems and find solutions within the Quarrying industry, please register your interest and we will get in touch.
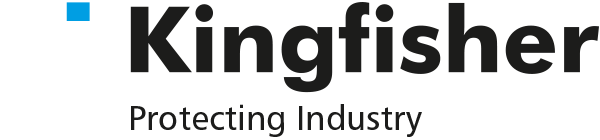
Asset integrity experts
In identifying all relevant wear criteria and referencing a huge portfolio of wear protection materials and techniques, Kingfisher is able to make sound recommendations supported by firm performance guarantees. This option reduces the inherent risk of uneconomic investment as the costs of replacement can sometimes outweigh the initial CAPEX cost.
For more information about how Kingfisher Industrial assists the global Quarry & Mineral Processing industry, have a read through our industry specific brochure and get in touch.
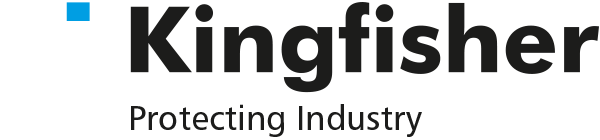
Wear Protection
Kingfisher offer a full range of ceramic, metallic and polymer lining systems. With our experience protecting process plant and equipment in many industrial applications and the performance knowledge of the materials we provide we offer a totally unbiased solution for each individual application.
Ceramic
Metallic
Polymer