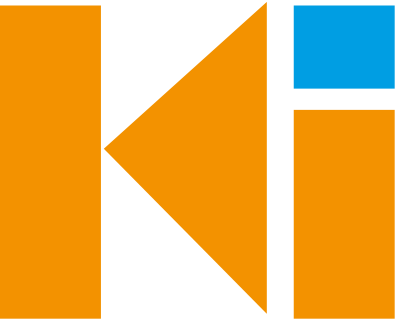
Wear Resistant Systems for Oil Extraction & Processing
Maintain plant efficiency and integrity with Kingfisher Industrial
Equipment Abrasion – we understand the pain
Albeit refined to an easily handled liquid or oil, the operation of extracting the resource from drilling wells both on and off shore and undertaking the process of refining its elements incorporates a multitude of activities that has to consider critical issues such as the environment, safety, quality and off course the commercial reward. Like so many resources society depends upon today, the oil industry continually has to defend its actions despite the demand from its detractors. However, with continued investment in technologies to ensure cleaner, safer and more efficient operations, then keeping abreast with the implementation of best engineering practices bodes well for the industry.
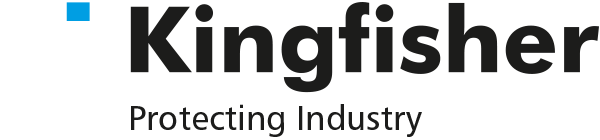
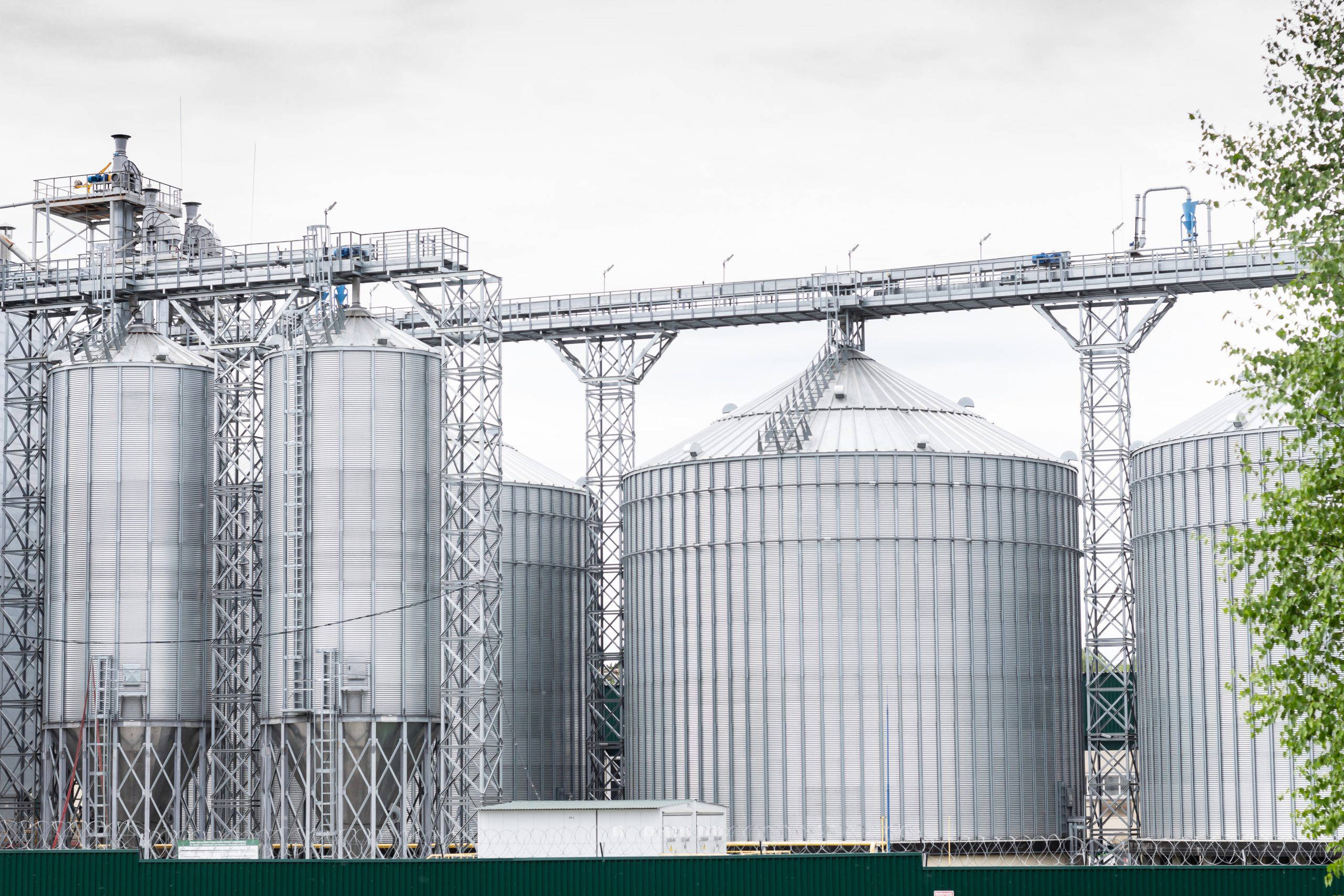
Ensure Continual Operation
During the separation phase of the extraction, equipment used to handle and recycle drilling mud from cuttings suffers from extreme abrasion due to the volumes handled and velocities conveyed. This equipment is critical to the process of continuing operation; therefore it is imperative that the equipment is both robust and protected to ensure continual operation. Utilising our range of both metallic and ceramic materials we have improved efficiency by protecting the conveying or moving parts that suffer from extreme abrasion, thus reducing the costs for replacement and downtime.
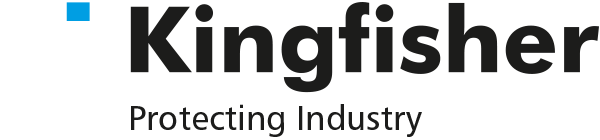
The Solution Providers
Within the refinery, the stages of separation, conversion and treatment consist of a multitude of activities and through each stage, the effects of those operations has on equipment used to pump, separate and process the oil takes its toll. With stresses such as mechanical, thermal and friction ever present, the attrition rate of the process is subjected to, has to be capable to withstand the most rigorous test and performance criteria in order to comply with the industries code of practice, ensuring both operator and environmental safety. Encompassing a system within these valuable assets can enhance the productivity and its service life leading to a significant return on investment when a cost versus payback formula is applied.
Protection over replacement
See below an example how Kingfisher Industrial can help with Wear Protection within the Oil Extraction industry
Problem
In the oil and petroleum extraction industry, the reliability and integrity of pipework systems are paramount for ensuring efficient operations. Pipelines play a crucial role in transporting materials such as crude oil, petroleum, and various fluids throughout the production site. However, the abrasive nature of these materials, along with the high-pressure pumping processes, can lead to significant wear and tear on pipework, resulting in costly maintenance and downtime.
Solution
Kingfisher collaborated closely with the production site’s engineers to design and install a customised wear-resistant lining system for the critical sections of the pipework network. Utilising advanced ceramic and polymer composite materials, the lining system was engineered to withstand the abrasive forces encountered during material transportation, while also providing chemical resistance and thermal stability.
Benefit
The successful implementation of wear-resistant linings has demonstrated their critical role in protecting pipework infrastructure in oil and petroleum extraction operations. By providing durable and reliable protection against abrasion, erosion, and corrosion, these linings enhance operational efficiency, safety, and reliability, ultimately contributing to the overall success and sustainability of production sites in the oil and petroleum industry.
Key Benefits
Enhanced Durability
Long term cost savings
Improved operational Efficiency
View more case studies
If you’d like to see more case studies showing how we Kingfisher help solve problems and find solutions within the Oil Extraction industry, please register your interest and we will get in touch.
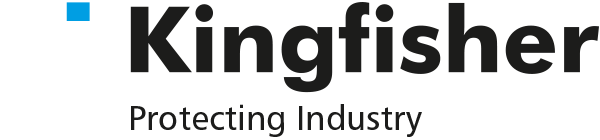
Wear Protection
Kingfisher offer a full range of ceramic, metallic and polymer lining systems. With our experience protecting process plant and equipment in many industrial applications and the performance knowledge of the materials we provide we offer a totally unbiased solution for each individual application.
Ceramic
Metallic
Polymer