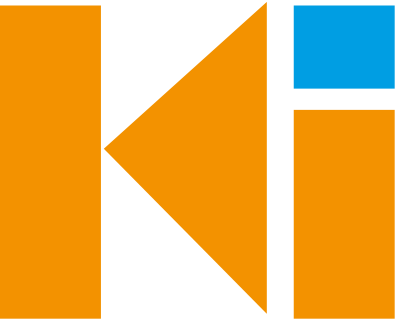
Wear Resistant Systems for Feed, Food & Beverage Plants
Maintain plant efficiency and integrity with Kingfisher Industrial
Plant degradation – we understand the pain
Processing and transferring the raw materials and finished product in animal feed plants brings large volumes of semi-aggressive media into contact with a variety of plant surfaces, with the capability to wear out hoppers, feeders, chutes and mixing equipment very quickly.
Repairing worn out chutes, ruptured pipelines and crumbling silos can become a routine activity on some sites; however this excess maintenance can be avoided by applying appropriate wear protection measures and materials.
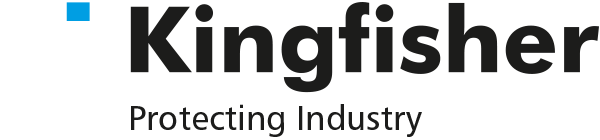
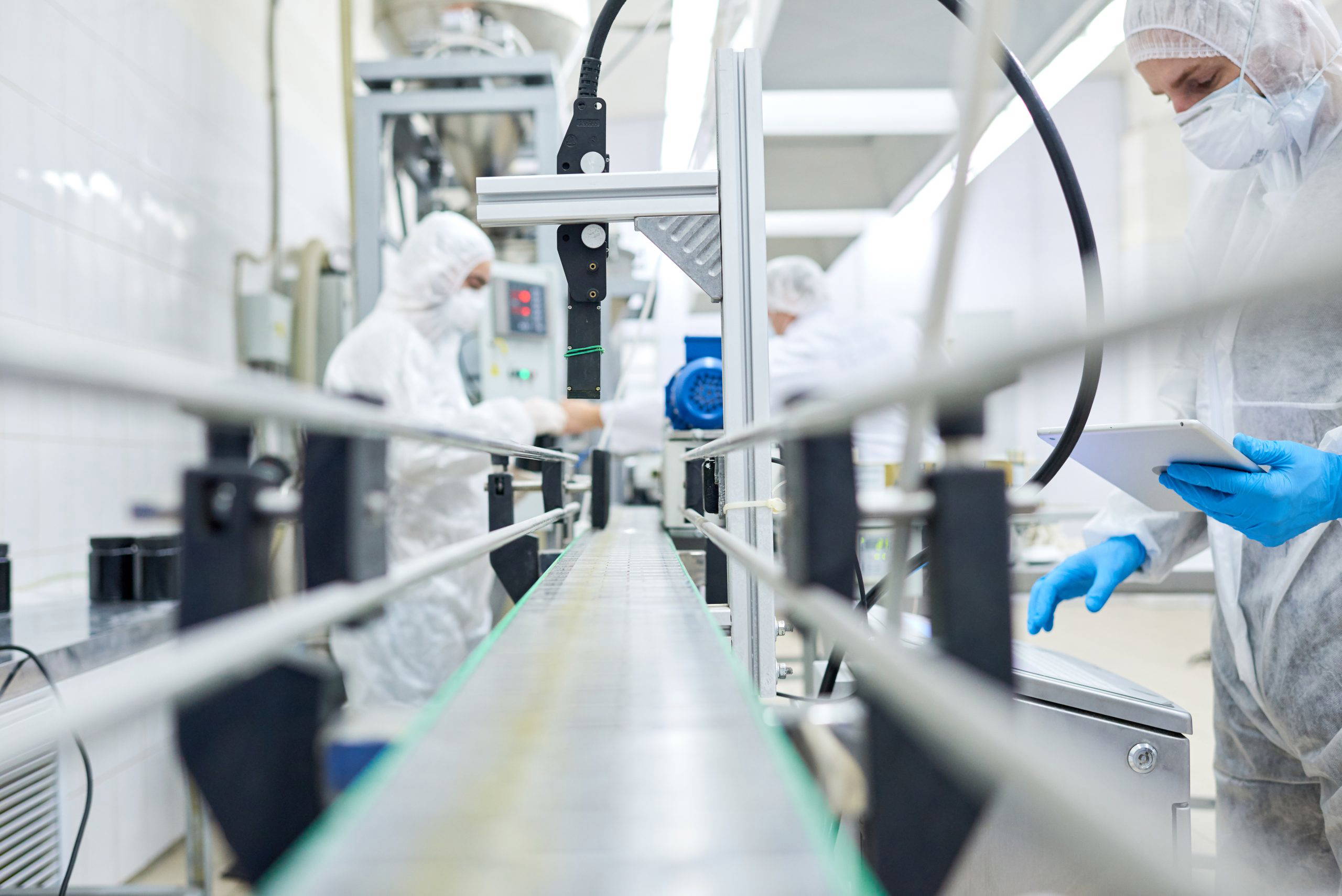
Reduce costs of repairs
Constant wear, leading to frequent repairs and maintenance of cyclones, separators, rotary vales and extrusion equipment can be avoided if the correct wear protection is applied. The result is to drastically reduce the cost of repairs on worn-out chutes and conveyors.
Handling solid and liquid ingredients together with binding agents makes the whole process of producing animal feed an activity where success depends on the equipment remaining reliable 24hrs a day in some instances. As with other bulk materials handling industries, the equipment needs to cater for many operational factors. If considered from the onset, these factors can be catered for and a design element introduced to compensate for potential wear problems.
Factors such as volumes, loadings, particle size and shape, viscosity and moisture content are typical criteria that must be addressed in order to eliminate potential problem wear areas. Selecting the right liner materials, hopper design and pipe installation can prevent the need for replacement and maintenance for up to 20 years.
Whether the feed is conveyed as dried, mixed or packaged, such processes create wear problems. Depending on the volumes and the operational regime, these materials will significantly reduce the value of your capital equipment if the plant is not wear protected for continual operation.
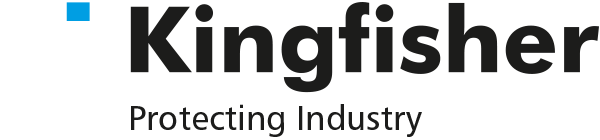
The Solution Providers
By introducing proven methods of design and plant maintenance, Kingfisher will add value and greatly reduce downtime and the need for on-going maintenance and repairs by eradicating material flow and plant degradation problems, either at the planning stage or at the production plant.
Eliminating these on-going wear and repair concerns allows the process to operate as designed, maximising its efficiency and the operational team’s resource capability allowing production efficiency improvement and improved ROI in the animal feed processing business.
Protection over replacement
See below an example how Kingfisher Industrial can help with Wear Protection within the Feed & Food industry
Problem
Soya bean processing plants encounter significant production challenges in handling and conveying bulk quantities of soya beans through various stages within their facilities. One such challenge is the wear and tear caused by the highly abrasive nature of the raw material, especially during the conveying process through transfer chutes.
Solution
Upon assessing the site and understanding the unique challenges faced by the client, Kingfisher proposed a tailored solution: The implementation of a wear-resistant lining system within the transfer chutes. This lining system not only aimed to protect the structural integrity of the chutes but also to meet the stringent requirements for food safety.
Benefit
Kingfisher recommended the use of their proprietary K-ALOX lining system, known for its exceptional wear resistance and FDA approval for use in food processing applications. The K-ALOX lining system was specifically engineered to provide a robust barrier against wear and tear while also contributing to a low-friction surface, thereby optimising the efficiency of the transfer process.
Key Benefits
Low friction lining system
Minimal cost to improve performance ratio
FDA Approved lining system
more examples
View more case studies
If you’d like to see more case studies showing how we Kingfisher help solve problems and find solutions within the Feed & Food industry, please register your interest and we will get in touch.
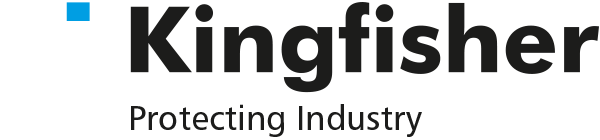
Wear Protection
Kingfisher offer a full range of ceramic, metallic and polymer lining systems. With our experience protecting process plant and equipment in many industrial applications and the performance knowledge of the materials we provide we offer a totally unbiased solution for each individual application.
Ceramic
Metallic
Polymer