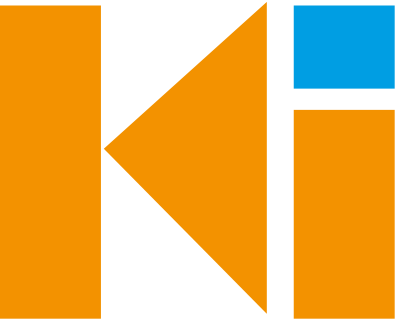
News from Kingfisher
Helpful articles delivered to you from Kingfisher Industrial.
The Strategic Value of MRO Projects in the Cement, Quarrying and Aggregates Sector
In the demanding world of cement, quarrying, and aggregate production, operational efficiency and equipment reliability are critical to productivity and profitability. Maintenance, Repair and Overhaul (MRO) projects play a pivotal role...
UK Cement Sector Under Strain Despite Industrial Strategy Commitments
The UK cement industry, essential to national construction and infrastructure delivery, is facing a sharp decline in domestic production, raising alarm among industry leaders despite new energy cost relief measures proposed in the...
Extending Equipment Lifespan with Wear Resistant Linings in the Cement and Aggregates Sector
The cement and aggregates industry is synonymous with abrasive environments, high-throughput operations, and continuous production demands. These factors make equipment longevity and operational reliability critical concerns. We understand these challenges. Our...
New Global Carbon Rating System for Cement and Concrete Launches
Pioneering Global Standard Promotes Sustainable Procurement in Construction. The Global Cement and Concrete Association (GCCA) has launched the world’s first Low Carbon Ratings (LCR) system for cement and concrete, a transformative step towards sustainable...
Transform Your Bulk Material Handling with Expert Wear Protection
Bulk Material Handling with Expert Wear Protection: Imagine your quarry, cement plant or asphalt facility running smoothly month after month. No emergency shutdowns. No material spillage. No constant repairs to worn equipment. Your maintenance team focuses on planned...
The Importance of Wear Resistant Pipework in Process Plants
In the demanding world of industrial processing, the integrity of pipework systems stands as a critical factor in maintaining operational efficiency. At Kingfisher Industrial, we've observed firsthand how wear-resistant pipework solutions...
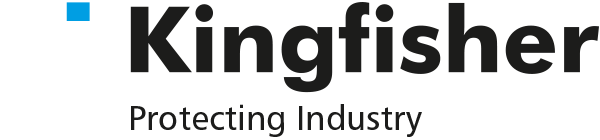
Wear Protection
Kingfisher offer a full range of ceramic, metallic and polymer lining systems. With our experience protecting process plant and equipment in many industrial applications and the performance knowledge of the materials we provide we offer a totally unbiased solution for each individual application.
Ceramic
Metallic
Polymer